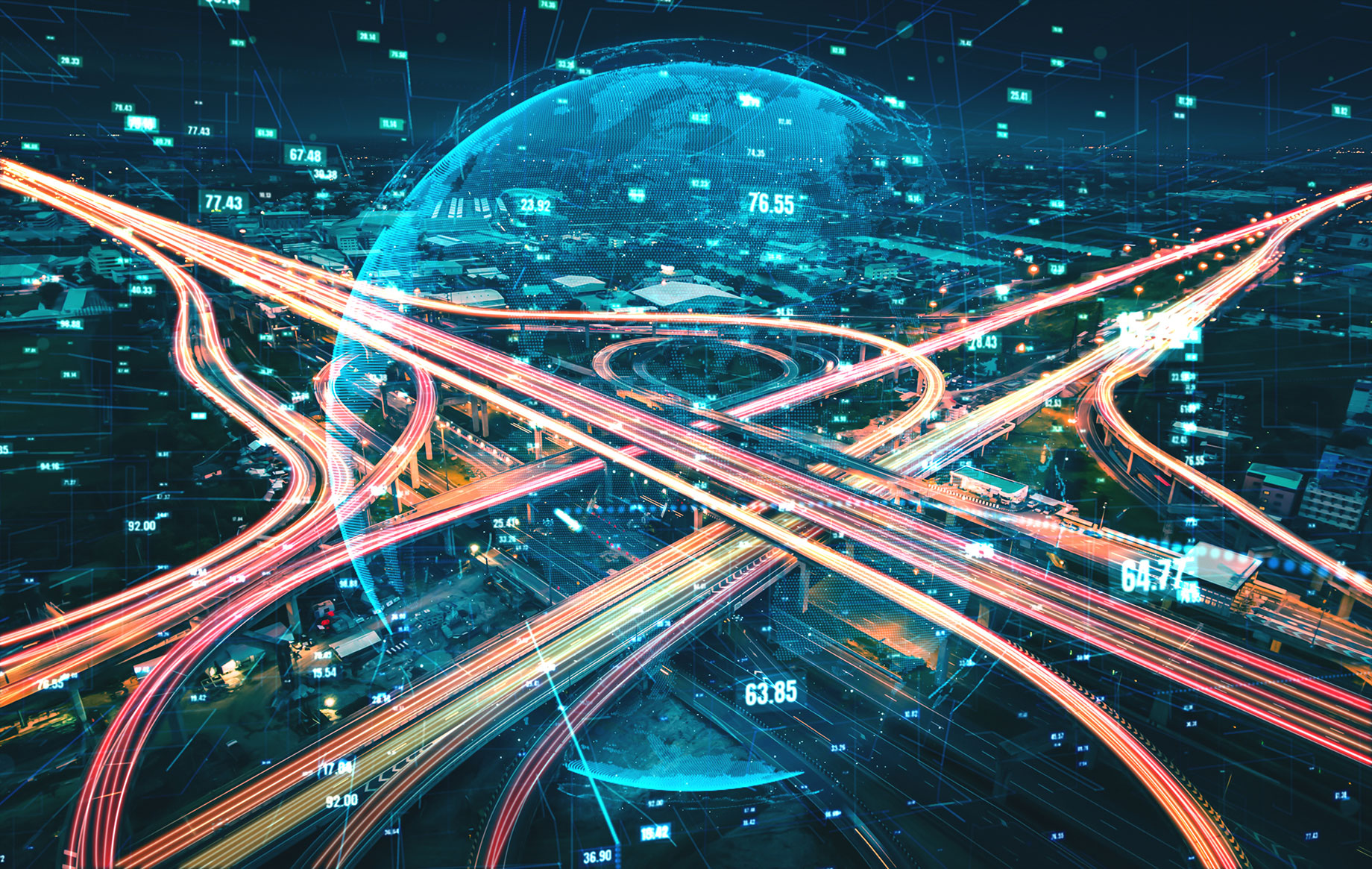
Outdated infrastructure drains resources and stalls progress. In fast-growing urban hubs and resource-tight rural zones alike, the pressure is on to build systems that keep up with changing needs. As expectations rise for faster turnarounds and lower overhead, smart infrastructure is no longer optional—it’s a strategic advantage.
Flexible, sustainable systems not only support current operations but also position businesses for long-term gains. Modular designs, efficient layouts, and scalable components reduce friction today while laying groundwork for tomorrow’s demands. With the right upgrades, facilities become more adaptable, resilient, and cost-effective for years to come.
Switching to a Busway System for Scalable Power Distribution
A ceiling-mounted busway system offers a smarter way to distribute power in dynamic environments. With modular plug-and-play units, teams can reconfigure layouts quickly—no major rewiring or downtime needed. As operations change, power access can shift just as easily, which helps avoid bottlenecks in warehouses, labs, or production areas.
Because the components are UL-certified, safety stays high while flexibility grows. Adding or moving branch circuits doesn’t interrupt the whole system, so updates happen faster and with less disruption. Maintenance is simpler, too—technicians can isolate sections without halting everything. A well-designed busway system cuts both labor and long-term infrastructure costs while supporting continuous adaptation.
Installing Cable Trays With Multi-Tier Routing for Mechanical Separation
Multi-tier cable trays organize power and data lines into separate, clearly defined paths—cutting down on clutter and helping systems run more smoothly. Physical separation limits signal interference, especially around sensitive equipment, while making routine inspections faster and less prone to errors. Dedicated tiers also simplify cable tracing and speed up diagnostics when issues arise. As facilities grow, new lines can be added without halting operations.
Overhead placement clears walkways, reduces tripping hazards, and frees up floor space for equipment or movement. With fewer cables underfoot, cleaning becomes simpler and safer. A well-designed tray system keeps wiring accessible, minimizes downtime during updates, and supports cleaner, more responsive work environments that can adapt easily to future changes.
Implementing Quick-Disconnect Utility Drops in Production Zones
Quick-disconnect fittings streamline tool changes and reduce downtime in production areas. Instead of rewiring or reconfiguring stations, teams simply unplug and switch tools at standardized drop points. This setup keeps workflows fluid and lets workers adapt quickly to shifting tasks.
Visual clarity improves with color-coded connectors, which support safety protocols and speed up training. New team members grasp the layout faster, making transitions smoother and reducing setup errors. For example, matching air or power tools to their sources becomes more intuitive. A well-designed quick-disconnect system keeps productivity high while maintaining an organized, flexible workspace.
Adopting Distributed Control Panels Near Work Cells
Placing control panels near work areas helps speed up maintenance. Having them close by makes troubleshooting faster, which means less downtime. Teams don’t have to waste time walking across large spaces to fix problems. For example, technicians working on packaging lines can immediately address a motor issue without leaving their zone. They can respond more quickly when something needs attention.
Modular parts make it easy to update or add new equipment. Installing things step by step helps avoid big disruptions. Instead of doing full system overhauls, gradual upgrades fit better with ongoing work. Thoughtfully placing control panels helps changes go more smoothly, keeping workflows steady and reliable.
Mounting Lighting on Unistrut Grids for Independent Adjustment
Unistrut grids give facilities full control over lighting placement without requiring structural changes. Lights can be repositioned easily to support shifting workflows, making this setup ideal for production lines, assembly areas, and labs where tasks change frequently. The ability to move fixtures without rewiring or reconstruction saves time and avoids costly disruptions.
Built-in raceways help contain wiring, reducing clutter and lowering the risk of cable snags during equipment moves. In spaces like repair bays or training zones, tool-free adjustments let teams modify lighting on the fly to suit specific tasks. This flexibility improves efficiency, supports safety, and scales with your facility’s changing needs.
Smart infrastructure upgrades don’t have to be massive to deliver real impact. Start with lighting, control panels, or modular power systems—small changes that bring visible results quickly. Improvements help teams cut downtime, lower costs, and respond faster to shifting demands. An organized layout, safer workflow, and quicker access to utilities can transform daily routines. Teams gain more control over space, equipment, and energy use. Choose one upgrade that addresses a current challenge, and build from there. Momentum grows fast when changes solve real problems from day one. Even a single smart improvement can lead to lasting operational advantages.