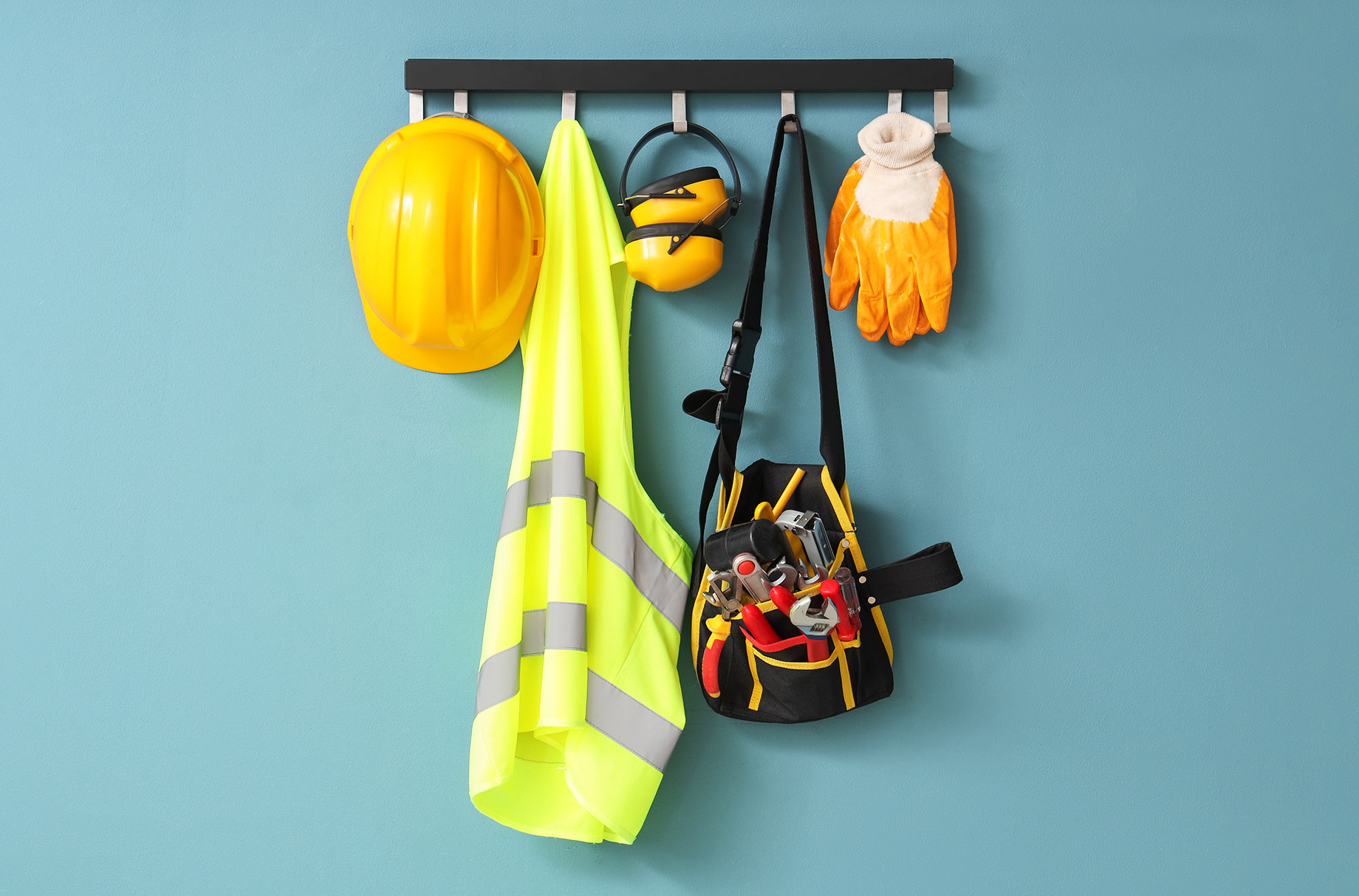
Personal protective equipment (PPE) is self-evidently a good thing for job sites with present hazards. However, many employers misunderstand the fundamentals of PPE or mishandle it in critical ways that prevent it from being effective on the job-site.
How should you approach managing PPE on your job-site?
The Impact of Better PPE Management
Why is PPE management so important for construction businesses?
- Employee safety. First and foremost, PPE management can greatly increase employee safety. You won’t be able to eliminate or avoid every possible hazard on the job-site, so PPE is a meaningful final line of defense. In some cases, it can save your employees’ lives, and in others, it can protect them from serious injury.
- Legal and regulatory compliance. Proper PPE management also ensures legal and regulatory compliance. Your business is likely subject to many rules and ordinances about job-site safety, and a consistent, thoroughly documented approach to managing PPE can help you remain in compliance with them.
- Cost savings. Good PPE management can also help you save money. Not only will you save money on PPE itself and on the costs related to managing it, but you’ll also save money on insurance and legal costs, as well as other expenses in the realm of hazard management.
- Morale and confidence. Incidentally, PPE management can also boost morale and confidence among your employees. This can, in turn, boost both productivity and employee retention.
Hazard Assessment
In a way, PPE should be treated only as a last resort. Accordingly, the first phase of your PPE management should be focusing on using it only when it’s required. Instead, you should focus on eliminating hazards, replacing hazards, isolating people from the hazard, or changing the way that people work in your environment. Only when these initiatives fail should you break out the PPE to protect people from the unavoidable hazard.
PPE Acquisition
Next, you can work on your PPE selection and acquisition. There are many types of PPE available, and within each category are likely hundreds, or even thousands of individual options. When exploring the possibilities for your job-site, focus on:
- Types of protection offered. For each item of PPE, you should review the type of protection offered. Exactly what types of hazards does this equipment guard against, and how effective is it in that application?
- Safety ratings. Similarly, you should explore safety ratings and objective metrics that can teach you about how this piece of equipment performs. As a simple example, different types of hearing protection can reduce the functional decibel level of various noises by different amounts. You’ll need to choose the right piece of PPE for the job.
- Availability and consistency. You may also want to consider the overall availability and consistency of availability for this product. Is this something that you’ll need to buy regularly? And if so, do you want to make sure you keep getting it from the same provider?
- Prices. Of course, you’ll also need to think about price. It may not be worth buying the most expensive item on the market if there is a less expensive alternative that offers a similar level of protection. That said, you should never sacrifice employee safety just to save a few dollars.
Employee Education and Training
It’s also important to educate and train your employees, so they take PPE seriously and use it correctly. Focus on helping your employees in:
- Understanding the hazards. The better your employees understand the hazards they’re dealing with, the more likely they will be to avoid those hazards and use PPE responsibly.
- Becoming familiar with proper PPE use. It’s also important to use PPE properly, ensuring an adequate fit and using it for the right applications. Verify that all of your employees know how to use PPE well.
- Taking safety seriously. Safety culture also matters. If your employees don’t value safety or take it seriously, they won’t use PPE consistently or effectively.
Maintenance and Inspections
It’s a good idea to conduct regular inspections and practice maintenance when needed, ensuring that your PPE is always in adequate condition when it’s made available for your employees. Be as consistent as possible in these processes so that nothing slips through the cracks.
Documentation
Document everything related to your PPE management strategy. This way, you can minimize risks to your organization and conduct more effective root cause analyses when necessary.
Recurring Audits
Finally, it’s a good idea to put some recurring audits in place. This way, you can regularly review how your PPE is managed and used on the job-site, so you can keep making improvements in the future.
With these PPE management strategies in place, you should have reliable protective equipment consistently available for your employees. Ultimately, that’s going to keep your employees safe, save your business money, and help your business grow in the long term.